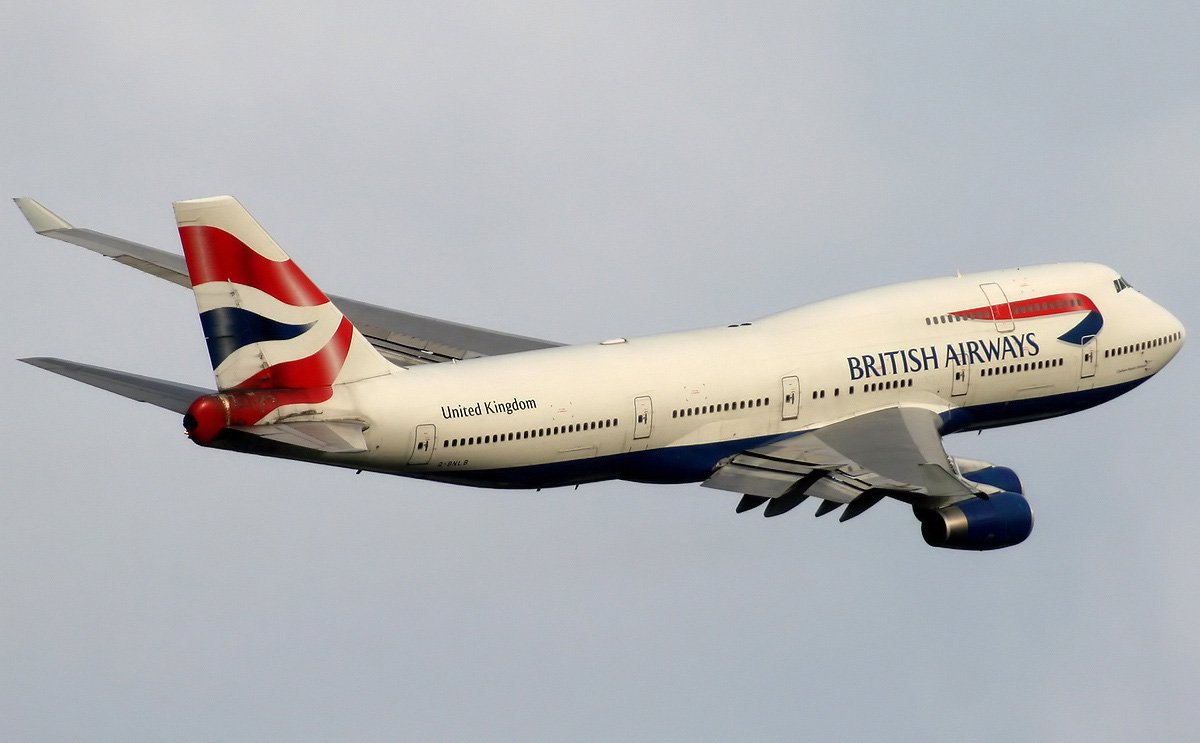
Boeing 747.
SPECS
ASSEMBLY
INTERIOR
HISTORY
ORDERS
An Air New Zealand Boeing 747-400 departs Christchurch.
The Boeing 747 was the Queen of Skies for near on 50 years and has now all but disappeared as the large, more economical twin jets take over. This demise was also hastened by the downturn in travel caused by Covid 19.
Being the first wide-body aircraft ever built, the Boeing 747 was the result of the demands of growing trans-continental(USA) and trans-oceanic travel markets in the 1960s.
The Boeing 747 on its main deck has two aisles where typically the economy cabin has a seat configuration of three seats on each window side and four seats in the centre, known as 3-4-3. The distinctive bubble atop the front of the fuselage accommodates the flight deck and in the first 747s during the 1960s, there would be a first-class lounge in the rear of the bubble which was accessed by a circular staircase.
Following the oil crisis of the early 1970s, many airlines opted for foregoing the upstairs lounge and replacing this with extra seating to try and offset the higher fuel-driven operating costs.
A Silk Way Airlines Azerbaijan Cargo Boeing 747-400 Registration 4K-800 demonstrates the cargo version of the Boeing 747.
The fast-paced growth of long-distance travel that was present in the 1960s drove two different trains of thought. Firstly how to move more people at once, and secondly how to move them more quickly.
With this in mind, the Boeing 747 was designed to carry large amounts of passengers. To allow for contingencies should the second become the future focus of commercial aviation, and we have to remember that supersonic flight was a reality at that time, the 747 was also designed to be capable of carrying large volumes of cargo when configured as a freighter.
For this reason, the flight deck was housed in a bubble atop the main fuselage so as to enable a nose cargo door to be installed with a clear passage to the main deck. Should the market fall out of the high-volume passenger market due to Super Sonic Transport (SST) becoming the norm, then the 747 still had a market as a freighter.
The Boeing 747 121 prototype takes to the skies for the first time. What a sight that would have been.
The introduction of this much larger aircraft caused its own headaches for airport operators, for instance, runways had to be strengthened. Boeing for their part equipped the 747 with 18 wheels to enable a better distribution of weight. Terminal gate areas also had to be widened to accommodate the greater wing span, as well as passenger assembly areas now needed to be able to accommodate two to three times as many passengers as previously.
The Boeing 747 design was such a departure from the technology then in use that it took 75,000 engineering drawings and 15,000 hours of wind tunnel testing to come up with the first Boeing 747 prototype. Five aircraft then completed a ten-month 1,500 flying hour test program to gain certification for commercial operation.
It is interesting to note that the entire Boeing 747 fleet has logged 42 billion nautical miles (77.8 billion kilometers) which is equivalent to 101,500 return trips from Earth to the Moon. On the trips that make up that distance, more than half of the Earth's population has been carried, a total of 3.5 billion people.
Lufthansa Boeing 747-8 Registration D-ABYM. Lufthansa was the launch customer for the Boeing 747-8i. The 8i stands for Intercontinentalwhich denotes the passenger version. The much more popular freight version is the Boeing 747-8F.
The 747 8, the final model, is an evolutionary follow-on from the 747 400, rather than a revolutionary jump. Some of the new technologies used in the Boeing 787 Dreamliner have also been used in the 747 8, such as LED lighting in the cabin, larger passenger windows, and partial fly-by-wire systems. Fly-by-wire means that control input on the flight deck is transmitted by electric wire to actuators on the control surfaces rather than heavier hydraulic systems.
The fuselage length of the Boeing 747 has not changed since 1968 other than the shorter Boeing 747SP (Special Performance) which was popular with a few airlines that required longer-range aircraft like QANTAS, Iran Air, and South African Airways. The Boeing 747 8 is only the second to depart from the standard fuselage length by adding 5.6 metres (18.3 ft) to achieve an overall length of 76.25 metres (250ft 2in). This makes Boeing 747 8 the longest passenger liner in the world-beating Airbus A340-600 by 7.5cm (3in), and the largest passenger liner ever produced in the USA.
If building the world’s biggest airliner was going to be a challenge, then no less so was the challenge of building a plant large enough to accommodate the assembly line.
After investigating sites in 50 different cities around the United States, Boeing settled on a site around 48 Km(30 miles) north of Seattle, Washington in June 1966. The location was adjacent to Paine Field, a military base near Everett. Once the 315.65-hectare (780 acres) site was acquired, it had to have 3.1 million cubic metres (4 million cubic yards) of soil moved before the building could commence.
Construction of the plant, which is the largest building by volume ever built, had to be completed urgently as the development of the Boeing 747 was gathering pace. The first mock-up of the Boeing 747 was completed before the roof of the plant was even completed.
ASSEMBLY
Boeing B747-400 assembly plant.
Ever since 1914 when Henry Ford pioneered the moving assembly line for the construction of his Model T, this process has been the mainstay of mass production in the automotive and other industries. The concept has remained basically unchanged in the ensuing years other than technological advancements.
The gains in efficiency, accuracy, and speed to completion are self-evident. Boeing implemented such a process for the assembly of the Boeing 747. The design of the process is quite mind-boggling, and it is constantly being re-evaluated. Over the last decades software simulation programs have been instrumental in perfecting processes and enabling the movement from a 24-day construction period per unit toward a target of 18 days. Having the processes in order so that workers are not trying to access the same area to perform different tasks.
The forward fuselage section of the Boeing 747 400 is married to the centre section.
For several decades technicians worked from stations located along the walls of the factory and stepped up to the aircraft as it entered their area. Now they stay with the aircraft as it moves with all the necessary tools at hands reach. Engineers are a radio call away.
This methodology does a lot to reduce workshop clutter and inventory, thereby improving speed and cost.
Boeing 747 400 tail section.
Boeing 747-8 Assembly
In the construction of the Boeing 747 8, nothing is actually manufactured in the Boeing plant, it is simply an assembly location. Parts for the Boeing 747 8 are made all over the world, such as seats from Germany, wing elements from China, and flaps from Australia. It takes around 6 million parts to create one aircraft, but very few of those are stored in the plant.
Boeing uses a "Just in Time" system which means that parts arrive at the factory just prior to being required for a particular phase of construction. This is closely monitored by computer inventory systems which flag if a part that is critical to the next phase has not yet arrived. It sometimes happens that a part does not arrive on time but it is rare. For example, the General Electric engines that are valued at $20 million each don't arrive until a day or two before the completed plane is due to roll out of the factory.
Has anyone seen a plane that needs a ride? The full set of landing gear for a Boeing 747 8 is delivered and ready to attach.
The assembly process begins with the wing, the most critical part of the aircraft. A quarter of the factory floor space is given over to the construction of the wings. The wing starts by being stood on its edge so that workers can start affixing the ribs and skin to the main spar. In the factory, you will not see one robot. Each aircraft is built by hand, so each of the fasteners is attached by a worker to a very strict tolerance and then the work is rechecked.
The fuselage is assembled in three main pieces, the nose section, the centre section which includes the wing box and the after section.
The nose section is created in one piece whilst the middle and after sections are assembled upside down to start with. They are then turned 180 degrees on a reel-type device which allows the workers easy access to all parts with the final part being the roof construction.
Boeing 747-8i assembly mating fuselage parts together.
The most critical part of the whole operation is the marrying of the three fuselage pieces together. This operation is usually performed in the wee small hours of the morning when the fewest amount of workers are on the factory floor. It is a very exacting process and requires a high amount of coordination and concentration.
Once the aircraft pieces are married together, a very thorough inspection is carried out to check no parts have been left behind. Mirrors and flashlights are used to look into every nook, cranny, and cavity, searching out even the smallest nut or bolt. This is known as Foreign Object Debris(FOD). Any of these that ended up falling in the wrong place could spell disaster through power short-outs or similar.
Once the aircraft is put together, heavy concrete blocks are hung from each of the engine pylons to simulate engine weight. Without these, the aircraft would sit back on its tail. The aircraft is now ready to leave the factory, the onboard flight system and electrics have been tested and now the engines need to be mounted. Each $20 million engine weighs in at around 7 tonnes and is attached by eight bolts. The tolerance for the fastening of these bolts is extremely critical. The forward bolts are designed to sheer off before the rearmost, so in the event of an engine coming off, it will drop by the front first and away from the wing as opposed to going up and over and more than likely through the wing. A comforting thought.
A Lufthansa Boeing 747 8 Intercontinental is ready to leave the factory for the paint shop with her GENx engines attached.
The aircraft is now wheeled out of the factory and off to the paint shop. Here they first remove the layer of green vinyl material which has been in place throughout the construction to protect the skin in the factory. The bright and shiny metal is revealed and now painting the colours of the airline customer begins.
The thickness of the paint coat is strictly controlled so that it isn't so thick that metal corrosion can't be detected as well as not adding too much weight to the aircraft and thereby increasing fuel burn. The weight of the paint is around 500kg which is the same weight as 5 to 6 passengers. It will be 4 years before a repaint will be required.
The Boeing plant in Everett, Washington State. The largest building by volume on the planet with the largest murals on the doors.
The design and building of the Boeing 747 was an audacious leap forward in aviation. The demand to relieve congestion at airports struggling with the influx of a growing travelling public was to be solved by offering fewer aircraft with higher carrying capacity. An aircraft with a carrying capacity double that of the existing workhorses, the Boeing 707 and Douglas DC8, was required. Thus the Jumbo Jet was born. Let's take a look at the Boeing 747 Specs to better understand this Queen of the Skies.
Strangely enough, it wasn't the extra carrying capacity that attracted early customers of the aircraft, but longer range capabilities compared to other aircraft of the day.
The ability to consider designing such a large aircraft was made possible by the introduction of the High By-pass Turbo Fan engines that were able to deliver much higher thrust at a much-reduced fuel burn rate compared to pure jets in use at the time.
SPECIFICATIONS
A Lufthansa Boeing 747-200 taking off in Los Angeles LAX.
The four-engined Boeing 747 was designed to be the safest airliner so far built. Redundancy was in place for systems such as hydraulics, where a backup was available should the main system fail. There were dual control surfaces to enable the continued control of the aircraft should any of the surfaces fail. There were four main landing gear bogies each with four wheels. This was not only to spread the weight of the aircraft more evenly, but the 747 was capable of landing on two opposing bogies if necessary.
Everything about the 747 compared to other aircraft in use at the time of its initial launch, was on a grand scale. For instance; 147,000 pounds (66,150 kg) of high-strength aluminium is used in its construction, 171 miles (274 km) of wiring along with 5 miles (8 km) of tubing is used, and six million parts are used, half of which are fasteners.
Evolution of the Boeing 747. The 747-SP and the 747-8i are the only variants to have departed from the original fuselage length.
Boeing 747 Specs Table.
Boeing 747-100 | Boeing 747-SP | Boeing 747-200 | Boeing 747-300 | Boeing 747-400 | Boeing 747-8i | |
---|---|---|---|---|---|---|
Range | 9,800 Km (6,100 M) | 12,320 Km (7,650 M) | 12,700 Km (7,900 M) | 12,400 Km (7,700 M) | 13,450 Km (8,354 M) | 14,430 Km (8,966 M) |
Seating | 3 Class 366 2 Class 452 |
2 Class 331 | 3 Class 366 2 Class 452 |
3 Class 412 2 Class 496 |
3 Class 416 2 Class 524 |
Max 605 3 Class 467 |
Length | 70.6 Mtrs (231 Ft 10 In) |
56.31 Mtrs 184 Ft 9 In |
76.25 Mtrs (250 Ft 2 In) | 70.6 Mtrs (231 Ft 10 In) |
||
Wingspan | 59.6 Mtrs (195 Ft 8 in) | 64.4 Mtrs (211 Ft 5 in) | 68.44 Mtrs (224 Ft 7 in) | |||
Tail Height | 19.30 Mtrs (63 Ft 5 in) | 20.06 Mtrs (65 Ft 10 in) | 19.30 Mtrs (63 Ft 5 in) | 19.30 Mtrs (63 Ft 5 in) | 19.40 Mtrs (63 Ft 8 in) | 19.35 Mtrs (63 Ft 6 in) |
Cabin width (Interior) | 6.1 Mtrs (20 Ft) | |||||
Freight (underfloor) LD-1 | 173.3 M3 (6,190 F3) 30 x LD-1s |
TBA | 173.3 M3 6,190 F3 30 x LD-1s | 170.5 M3 (6,025 F3) | 161.5 M3 (5,705 F3) | |
Typical Cruise Speed at 35,000' | Mach 0.84 555 MPH / 895 KPH |
Mach 0.88 614 MPH / 990 KPH |
Mach 0.84 555 MPH / 895 KPH |
Mach 0.85 565 MPH / 910 KPH |
Mach 0.85 565 MPH / 910 KPH |
Mach 0.92 614 MPH / 988 KPH |
Maximum Taxi Weight (MTW) | 334,750 Kg (738,000 lbs) |
318,875 Kg (703,000 lbs) |
379,202 Kg (836,000 lbs) |
379,202 Kg (836,000 lbs) |
397,800 Kg (877,000 lbs) |
- |
Maximum Takeoff Weight (MTOW) | 333,400 Kg (735,000 lbs) |
304,000 Kg (670,000 lbs) |
374,850 Kg (833,000 lbs) |
374,850 Kg (833,000 lbs) |
396,890 Kg (875,000 lbs) |
447,696 Kg (987,000 lbs) |
Maximum Landing Weight (MLW) | 265,350 Kg (585,000 lbs) |
215,465 Kg (475,000 lbs) |
285,762 Kg (630,000 lbs) |
285,762 Kg (630,000 lbs) |
285,762 Kg (630,000 lbs) |
312,000 Kg (688,000 lbs) |
Maximum Zero Fuel Weight (MZFW) | 238,816 Kg (526,500 lbs) |
192,776 Kg (425,000 lbs) |
247,207 Kg (545,000 lbs) |
247,207 Kg (545,000 lbs) |
246,754 Kg (544,000 lbs) |
295,000 Kg (651,000 lbs) |
Maximum Fuel Capacity | 183,380 L (48,445 US G) |
178,000 L (47,210 US G) |
199,158 L (52,410 US G) |
199,158 L (52,410 US G) |
216,840 L (57,285 US G) |
238,610 L (63,034 US G) |
Engines and Thrust | Pratt & Whitney JT9D-7A Thrust 46,500 lb (20,925 kg) Rolls-Royce RB211-524B2 Thrust 50,100 lb (22,545 kg) GE CF6-45A2 Thrust 46,500 lb (20,925 kg) |
Pratt & Whitney JT9D-7R4W Thrust 46,500 lb (206.8 kN) Rolls-Royce RB211-524C2 Thrust 46,500 lb (206.8 kN) |
Pratt & Whitney JT9D-7R4G2 Thrust 54,750 lb (24,635 kg) Rolls-Royce RB211-524D4 Thrust 53,000 lb (23,850 kg) GE CF6-50E2 Thrust 52,500 lb (23,625 kg) |
Pratt & Whitney JT9D-7R4G2 Thrust 54,750 lb (24,635 kg) Rolls-Royce RB211-524D4 Thrust 53,000 lb (23,850 kg) GE CF6-80C2B1 Thrust 55,640 lb (25,040 kg) |
Pratt & WhitneyPW4062 Thrust 63,300 lb (281.57 kN) Rolls-Royce RB211-524H2-T Thrust 59,500 lb (264.67 kN) GE CF6-80C2B5F Thrust 62,100 lb (276.23 kN) |
GEnx-2B67 Thrust 66,500 lb (296 kN) |
Boeing 747-100 | Boeing 747-SP | Boeing 747-200 | Boeing 747-300 | Boeing 747-400 | Boeing 747-8i |
In 1963 Boeing was among a group of plane makers that were competing for a military contract to build a very large transport. One of the main requirements for the military transport design was for a nose loading cargo door with clear access to the main deck. The Boeing design featured a bubble atop the fuselage forward of the wing leading edge.
The contract went to Lockheed and General Electric to build what was to become the C5 Galaxy.
During this time, commercial aviation was growing at a rapid pace. The jet age was finding its feet with the very popular Boeing 707 and Douglas DC8 being the workhorses of the day. Juan Trippe of Pan Am, one of Boeings biggest customers, approached Boeing to press them to look at building an aircraft twice the size of the 707 and DC8. Trippe advocated that a larger aircraft would be the solution to the congestion at airports, reducing the number of relatively smaller aircraft required to move the same amount of people.
History.
The first Boeing 747 100 rolls out of the factory. Note the logos of all the airlines who had ordered this aircraft and the cabin crew uniforms of each of these carriers.
Pan American Boeing 747-100. Note the few windows in the upper deck, this area was a lounge not for seating.
In 1965 Boeing put together a design team to work on the new airliner which was already given the Boeing 747 designation. The proposal Boeing had put forward for the military transport, the CX-HLS, was taken as a starting point. Some features were retained, but others such as the high-wing design were discarded. The design also had to be future-proof.
At this time in aviation, it was felt that supersonic travel had every chance of becoming the norm, so Boeing had to take an each-way bet. The design team for the Boeing 747 had to come up with an aircraft that met the requirements of airlines that wanted mass passenger movement, but at the same time had the ability to be an effective freighter.
Pan Am became the launch customer for the Boeing 747 in April 1966 by ordering 25 Boeing 747 100s. Being involved from the beginning of the design and development of the Boeing 747, Pan Am influenced these phases more than any other airline before or since.
This Boeing 747 131, registration N93119, was the aircraft that flew the ill-fated flight TW800 from New York to Rome via Paris on 17 July 1996. The flight crashed into the ocean with 230 lives lost off the coast of East Moriches, New York. A short circuit causing a fuel explosion was determined to be the cause.
Initial designs of the 747 called for a twin-deck aircraft, with both decks running the full length of the fuselage. This gave a very effective increase in capacity, however, the ability to evacuate two decks of passengers was found to be not possible within the recommended 90-second limit. Boeing opted for a single main deck which was then widened from the standard economy configuration of the day of six across, three and three, with a single aisle to a twin-aisle layout with seating ten across in a three-four-three configuration.
One of the main enablers that made such a larger aircraft possible was the advent of high-bypass turbofan engines. General Electric applied the principle to the C5 Galaxy project. The high bypass turbofan delivered twice the power of turbojets which were in use at the time and used one-third less fuel. Pratt and Whitney were also working on this concept and in 1966 Pan AM, Boeing and Pratt and Whitney agreed to develop the JT9D as the powerhouse for the 747.
Boeing 747-284B of Olympic Airways registration SX-OAB.
The Boeing 747, since its inception in 1968, has been the workhorse for many of the world’s airlines.
Various improvements have been made to the basic design over the years as technology has advanced as well as the demands of the travelling public. For four decades the 747 reigned as the largest passenger airliner in the skies.
Global trends such as the advent of Low-Cost Carriers and higher fuel and other operating costs started to put pressure on plane makers to sharpen their pencils and work towards new designs that would not only be more fuel efficient but also comply with stricter noise reduction levels demanded at so many airports today.
The first commercial flight of the Lufthansa Boeing 747-8 lands at Washington DC, Dulles.
In the 1990s and into the new century, Boeing investigated different options such as the 747 500X and 747 600X which was a stretched version of the 747 using a derivative of the Boeing 777 wing. This was publicised at the Farnborough Airshow of 1996 but attracted little interest. The idea was shelved.
In 2000 Boeing offered a 747X which was a less dramatic change to the basic model with a stretched fuselage of some 263 ft (80.2 m). The wing span would be increased by inserting a segment at the wing root bringing the span to 229 ft (69.8 m). The pressure was on to compete with the proposed solution from Airbus, the Airbus A380.
Boeing 747 Notable Events. | |
---|---|
Date | Event |
1963 | The U.S. air-force commissions studies into a large transport aircraft capable of carrying over-sized cargo which cannot be accommodated by aircraft of the day. |
March 1964 | The outcome of the Air-force study was a requirement for the CX-HLS(Heavy Logistics System). |
1965 | Lockheed and General Electric are given the military contract to build the C5 Galaxy. |
1965 | Design study begins on a new airliner already designated 747. Pan Am and other airlines are invited to share their requirements. |
April 1966 | Pan Am orders 25 Boeing 747 100s on Boeings 50th anniversary. |
1966 | Boeing, Pan Am and Pratt and Whitney initiate the development of the JT9D engine for the 747. |
30 September 1968 | The first 747 was rolled out of the Everett plant in front of the press. |
09 February 1969 | The Boeing 747 made its maiden flight which had very pleasing results. |
13 December 1968 | One of the test aircraft was damaged when landing short at Renton. The outer landing gear was torn off as well as damage to two engine nacelles. |
1969 | Boeing took a 747 to the 28th Paris airshow where it was shown to the public for the first time. |
December 1969 | Boeing was awarded its FAA airworthiness certificate. The 747 was ready for commercial operations. |
15 January 1970 | The first delivery 747 for Pan am was christened by First Lady Pat Nixon. she was named Clipper Victor. |
22 January 1970 | Pan Ams' inaugural 747 flight took place from New York to London. It was delayed from the 21st of Jan due to engine overheating. |
February 1971 | The Boeing 747 200 was introduced into service. With more powerful engines and a greater Maximum Takeoff Weight, this variant had achieved a range of 6,000NM/11,000Km making it viable on international routes previously not possible with the 747 100. |
03 August 1973 | The first 747 100SR short range high seating capacity aircraft for Japan Airlines domestic market was rolled out. |
17 June 1975 | Boeing announced that the Rolls Royce RB211-524B would be an alternative choice of power-plant on the 747 200. |
1976 | The 747 SP was introduced into service. This variant was 48feet 4 In / 14.73M shorter than the 747 100 and was delivered to Pan Am and Iran Air in the same year. It operated the Tehran to New York route which was then the longest non-stop route. |
21 December 1978 | ANA (All Nippon Airways) received their first 747 100BSR a further development of the 747 100SR. This variant had a great Maximum Takeoff weight and it was strengthened for a high cycle (takeoff and landings) versus flying time ratio. |
20 June 1979 | First flight of the 747 100B which used the stronger air-frame of the 747 100SR with added fuel capacity to allow for a range of 5,000NM/9,300Km. |
11 June 1980 | Swissair places an order for the first Boeing 747 300 |
05 October 1982 | Maiden flight of the Boeing Boeing 747 300 |
23 March 1983 | Swissair takes delivery of their first Boeing 747 300 |
1985 | Work begins on the design of the Boeing 747 400. |
26 February 1986 | Maiden flight of the Boeing 747 100BSR, a high capacity variant with a stretched upper deck as added to the later 747 300. |
February 1989 | The 747 400 enters service with Northwest Airlines on the Minneapolis to Phoenix route. |
September 1989 | The 747 400 combi version enters service with KLM. |
September 1990 | The last 747 300 is delivered to Sabena. |
July 1996 | The 500X and 600X stretched 747s are proposed at the Farnborough Airshow with little interest shown. |
November 2002 | The 747 400ER enters service with QANTAS |
2004 | Early this year Boeing announced plans for the 747 Advanced which were eventually adopted. |
April 2005 | The final 747 400 is delivered to China Airlines |
14 November 2005 | Boeing announces plans for the Boeing 747-8. |
October 2006 | The design and configuration of the freighter version were firmed up. |
Boeing 747 Notable Events(continued). | |
---|---|
Date | Event |
August 2008 | Work begins in Everett on the first cargo version of the Boeing 747 8. |
14 November 2008 | Boeing announces delays to the program, brought about by changes to the design, limited resources and a strike. |
February 2009 | Lufthansa was the sole customer signed up for the passenger version, the Boeing 747 8 Intercontinental. Boeing reassessed the project. |
21 July 2009 | A photograph is released of an assembled cargo version plane. |
October 2009 | The first flight of the Boeing 747 8 Intercontinental(passenger version) is delayed until early 2010. |
12 November 2009 | Cargoluxs' first of thirteen planes is fully assembled and enters the paint shop. |
04 December 2009 | Korean Airlines orders five Boeing 747-8 Intercontinentals becoming the second customer for the passenger liner. |
December 2009 | First engine runs of the Boeing 747-8. |
08 January 2010 | Guggenheim Aviation Partners reduce their order of four freighters down to two. |
07 February 2010 | First high-speed taxi tests. |
08 February 2010 | The Boeing 747-8 Freighter made its maiden flight from Paine Field, lifting off at 12:39(12:39pm) and landing again at 16:18(4:18pm). |
15 March 2010 | The second Boeing 747-8 Freighter made its first flight from Paine Field to Boeing Field, and on to Palmdale to start tests with the first aircraft. |
17 March 2010 | A third aircraft joins the first two in testing. |
March 2010 | Korean Airlines adds two freighters to their firmed-up order. |
April 2010 | Possible defects in the upper fuselage with the potential to cause cracks found as well as a flutter caused by the main landing gear doors are found. |
19 April 2010 | Test aircraft No.2 is moved to Palmdale to complete engine tests in order to get the type certification. |
14 June 2010 | The initial flight-worthiness testing is completed and the FAA gives Boeing an expanded type of inspection authorisation. |
June 2010 | The three Boeing 747 8s clock up 500 hours in test flying but Boeing decided a fourth was required to complete testing on time. |
July 2010 | A Boeing 747 8 Freighter is displayed at the Farnborough Airshow. |
23 July 2010 | The fourth aircraft painted in Cargolux colours makes its first flight. |
21 August 2010 | A Boeing 747 8 Freighter takes off from Victorville, California weighing 1,005,000 pounds(455,860Kgs). Maximum take off weight is set at is 975,000 pounds (442,253 kg). |
30 September 2010 | Boeing announces another delay, with Cargoluxs' first aircraft to be delivered in mid-2011. |
20 March 2011 | First flight of the 747-8 Intercontinental passenger version at Everett. |
26 April 2011 | The second 747-8 Intercontinental passenger version makes its first flight. |
19 August 2011 | The Boeing 747-8 Freighter receives an amended type certificate jointly from the Federal Aviation Administration (FAA) and European Aviation Safety Agency (EASA). |
17 September 2011 | Cargolux states it would not accept delivery of the first two aircraft due for 19 and 21 September due to unresolved contract issues with Boeing. |
12 October 2011 | Boeing presents Cargolux with their first 747 8 Freighter. |
25 October 2011 | The 747-8 Intercontinental passenger version conducts tropical testing in Barbados. |
December 2011 | Lufthansa conducts evaluation tests with the 747-8 Intercontinental. |
14 December 2011 | The 747-8 Intercontinental passenger version receives type certification from the FAA. |
05 May 2012 | Lufthansa takes delivery of its first Boeing 747-8 Intercontinental. |
04 June 2012 | First commercial passenger flight of the Boeing 747-8 Intercontinental by Lufthansa from Frankfurt to Washington. |
29 July 2020 | Boeing confirmed that the production of of the 747-8 would end in 2022 when current orders were met. |
06 December 2022 | The last Boeing 747-8, a freighter for Atlas Air, rolled off the production line. |
At the time of its introduction, the Boeing 747 was radically different from anything that had previously been offered to the travelling public. Yes, Boeing had previously offered a twin-deck aircraft in the propeller-driven Stratocruiser, but the 747s upper deck was not originally designed to boost passenger seating so much as being a by-product of the elevated flight deck.
The 747 was the first wide-body commercial aircraft. Where the standard set by the incumbent intercontinental jets; the Boeing 707 and Douglas DC8, was to have an economy (coach) cabin layout of 3 seats either side of a single aisle, the 747 boasted twin aisles with 3 seats on each window side and 4 seats in the centre. This changed the look and feel of travel forever. The feeling of space in the larger cabin made long flights a bit more comfortable and less claustrophobic.
Cabin Interior.
An early Boeing 747 economy cabin. The feeling of space compared to the earlier single-aisle jets was appreciable.
Initially many airlines opted to use the upstairs bubble behind the flight deck as a first-class lounge. The area typically featured casual seating with a bar as shown in the Continental Airlines pictures above. As a result of the oil crises in the early 1970s, many airlines looked for ways to maximise revenue to cover the increased fuel costs. The upstairs bubble was converted to paid seating. Business Class was also introduced as a compromise between First and Economy (Coach) class, and often airlines would offer the bubble as their Business Class cabin.
As technology has improved along with changes in styles and fashions, so too the aircraft cabin selections of most airlines have. Gone now are the single large movie screens which adorned the front of each cabin. These have been replaced by most mainstream airlines with individual seat-back screens or screens that can be stowed away into a seat arm. Passengers are now able to make selections from a suite of entertainment options brought to their own individual screens.
Boeing 747 Continental Airlines upstairs lounge. The spiral staircase is on the left with the door to the flight deck straight ahead.
Toward the end of the life of the Boeing 747-400 many airlines were still heavily committed to the 747s in their fleets which still served them very well. In an effort to maintain their attractiveness to the travelling public, airlines, like QANTAS in Australia, had their 747-400s refurbished in styles influenced by Boeings’ new Dreamliner concept.
The benefits included a single beam seat design allowing more leg space in economy. Carbon fiber seat backs reduced weight and allowed for a thinner seat. Soft lighting and contoured panels made for a more spacious feeling cabin and offered a competitive comparison to newer jets being produced at that time.
United Airlines Boeing 747-422 Economy cabin. Prior to personal screens, inflight entertainment was shown on overhead and bulkhead screens. At the time of booking, you could ask the reservations agent what movie(s) would be shown on the flight.
On entering the new Boeing 747 8 Intercontinental, passengers will immediately know they are on a new aircraft. The interior concept is very much in line with the modern styles of the Boeing 787 Dreamliner. The airy swept-up Boeing Sky architecture gives a feeling of space.
The use of LED lighting, aside from the functional weight advantages as well as longevity, offers the ability to have smooth light transitions offering a more calm and soothing environment. The feeling is of being outdoors, the lighting and the sense of space. The 747 8 Intercontinental takes the technology and designs that make the Boeing 787 Dreamliner the sought-after aircraft of choice with passengers and runs with it.
Boeing 747-8 Intercontinental Business Class cabin downstairs. Note the stairway to the upper deck in background. Long gone is spiral staircase of old.
Orders and Deliveries.
The Boeing 747 encompassing the Boeing 747 100, 747 200, 747 300, 747 400, 747-SP, and 747-8 was produced over a period of over 50 years. Below we look at the launch customers of each of these variants as well as some other facts and figures.
Below are the launch customers for each 747 variant.
The first 747 delivered, the 747 100, was delivered on 15 January 1970. Najeeb Halaby, Chairman on Pan Am the launch customer, was on hand as first lady Pat Nixon christened her, Clipper Victor.
The first commercial service was from New York to London on 22 January 1970.
Both Pam Am and Iran Air requested Boeing to design a longer-range version of the 747 to accommodate the US Middle east routes. Pan Am was the launch customer with its first scheduled 747 SP service in 1976. Only 45 of the type were produced instead of the expected 200.
More powerful engines enabled the 747 200 to be used on international routes that were marginal for the 747 100. The type started service with Lufthansa in February 1971.
The Boeing 747 300 first flew on 05 October 1982 and was delivered to the launch customer, Swissair, on 23 March 1983. The most visible difference between the 300 and previous variants was the stretched upper deck.
The first Boeing 747-400 was delivered to Northwest Airlines who put it into service in February 1989.
Lufthansa took delivery of their first Boeing 747 8 Intercontinental (8I) on 25 April 2012.
Comparative Orders and Deliveries of the Boeing 747 Variants.
Boeing 747 Variant | Boeing 747 Orders | Boeing 747 Deliveries |
---|---|---|
747-100 | 275 | 250 |
747-200 | 408 | 493 |
747-300 | 81 | 81 |
747-400 | 544 | 442 |
747-400D | 20 | 19 |
747-400ER | 6 | 6 |
747-ERF | 40 | 40 |
747-400F | 130 | 126 |
747-400M | 64 | 61 |
747-8i | 58 | 48 |
747-8F | 142 | 106 |
Total | 1,768 | 1,572 |